
The Marine Coatings Market
The Marine Coatings Market
The Marine Coatings Market
The marine coatings market continues recovery from the impact of the pandemic, while travel restrictions continue to impact demand.
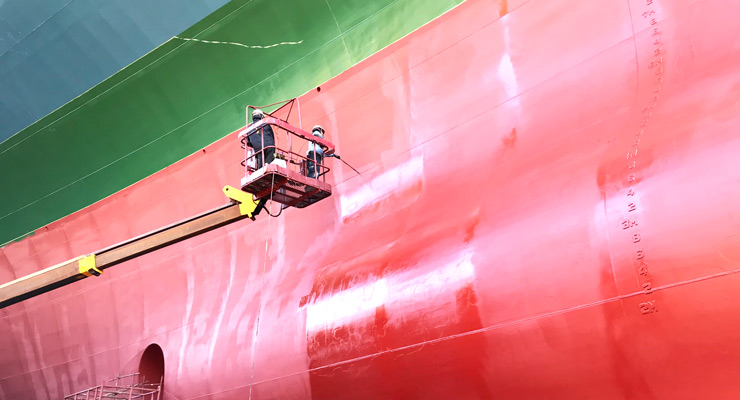
Nippon Marine Paint launched FASTAR series, an antifouling paint.
Kerry Pianoforte, Editor08.02.21
As the world continues to cautiously open back up, the marine coatings market is reporting signs of recovery.
“This year has been one of continuing recovery for the marine coatings market following the significant challenges posed by the outbreak of the pandemic in 2020,” said Christopher Birkert, Marine marketing manager at AkzoNobel. “As the global vaccine roll-out brings the virus under more control, global trade is increasing by 4%, resulting in more activity in the marine sector. We have seen a recovery of new build contracts – an increase of 4% overall – as well as a more positive sentiment from marine customers.
“We are proud to have supported our customers as we all navigated through the unprecedented events of 2020 together,” said Birkert. “What was really pleasing to see was that our customers continued to embrace innovation in pursuit of performance and more sustainable solutions in the yard and in operation. Drawing on the 140-year legacy of our International brand we continued to deliver cutting-edge products to meet this need, for example Intersmooth 7200Si, which has up to 40% lower VOC emissions per square meters applied than the nearest competitor, as well as the 90-month Intercept 8500, which delivers a guaranteed speed loss of 1.3% over the docking cycle.”
“Business has continued to move back to a normal state in 2021 and the high level of activity in the main shipping markets and in the newbuilding orders create a positive market recovery sign,” noted Ariana Psomas, PPG Global Segment director newbuild and dry dock. “For the most part we continue to remain optimistic about the industry’s resilience and we expect that it will continue to progress on a positive path.
“Above all, the COVID-19 pandemic has shown how quickly things can change and that, while change is difficult, PPG has proven time and again that we have the strength to manage through such situations,” she added. “With a proven track record of over 135 years, we have weathered many crises, and we consistently emerge stronger and better positioned to serve our customers.”
Some growth is being driven by a focus on sustainability and the need for products that reduce environmental impact and improve efficiencies.
“Recently, the management of shipping companies has become strongly Environmental, Social, and Governance (ESG)-oriented,” said Seiichiro Shirahata, president, representative director of the board at Nippon Paint Marine Coatings Co., Ltd. “Expectations for products and services that bring about environmental measures such as improved operational efficiency and fuel saving as well as economic effects are increasing. Adding to it, the International Maritime Organization (IMO) has set a medium-term target of reducing greenhouse gas emissions to half of the 2008 level by 2050. Furthermore, the organization has set a short-term goal of 40% fuel economy improvement by 2030 under the EEXI regulations from 2023. We will keep up with these trends.
“We have always faced environmental regulations to comply as we develop our marine paints,” added Shirahata. “Particularly the regulation in the 1990s on organotin compounds for antifouling paints on the bottom of ship and the EEXI regulation starting from 2023 are environmental regulations based on international treaties, and then we give first priority to comply with these regulations. In addition, there is environmental legislation enacted independently by the government as well, and we must comply with these regulations one by one.”
At AkzoNobel, sustainability is one of its core values and is integrated in everything they do. “Our approach to sustainable business will help us deliver tangible benefits for our customers, society, the environment and our business,” said Birkert. “As the paints and coatings industry’s leader when it comes to sustainability, we’re proud of our rankings across several indices as well as being recognized by EcoVadis with a platinum rating.
“Ocean preservation and supporting our customers and the industry in the carbon neutral journey are at the heart of the International brand and the ethos of AkzoNobel,” said Birkert. “We’re committed to providing our customers with the coatings and solutions to help address their environmental footprint reduction challenge beyond compliance and towards the shipping industry achieving its 2030 carbon neutral ambition.”
He cited Intersleek 1100SR as an example of the company’s commitment to developing products that not only meet the highest of environmental standards but also move the dial in terms of savings for fleet operators.
According to Birkert, it is one of the highest performance fouling control schemes on the market, It offers more than 10 years of performance without the requirement of a recoat and is proven to reduce paint consumption by 77%, VOC by 86% and decrease CO2 emissions by up to 110,000 tons over multiple operation cycles compared to biocidal Self Polishing Copolymer (SPC) technology.
“It is not always easy to predict exactly how regulation will change globally and we always try to match the highest possible standards,” said Birket. “Many countries around the world are looking harder at ways to improve sustainability through legislation. For example, China is looking very strongly at controlling emissions from industry while Korea has insisted that by 2020, 60% of all coatings to ballast tanks are solvent-free.”
“The shipping industry faces a formidable challenge in achieving compliance with the new environmental regulations set by the IMO and adopted in June 2021, which require drastic reductions in both carbon emissions and carbon intensity,” noted Psomas. “The ability to achieve reductions of this magnitude will require new fuels, new vessel designs and installation of energy efficient technologies to achieve radical improvements in operating efficiency.”
According to Psomas, the use of innovative energy efficient technologies is critical for improving operational performance. “The IMO has published a list of approved Energy Efficiency Technologies among which, low friction coatings have been recognized as a technology that can directly shift the power curve.”
In the area of low friction coatings, she noted that studies have concluded that silicone technology stands out compared to antifouling technologies with the ability to significantly decrease hull friction resistance. PPG’s proprietary biocide free silicone technology, PPG SIGMAGLIDE, has been shown to contribute in achieving these targets by reducing the vessel’s power consumption up to 10% and overall emissions during operation by up to 25% compared to a conventional antifouling technology.
Impact of COVID-19
Travel restrictions related to COVID-19 continue to present challenges to the marine and coatings market.
“A significant hurdle has been global travel restrictions that prevented crews and owner representatives from moving around freely to inspect vessels and plan work,” said Birkert. “As during the shipping crisis of 2010, we helped to support our customers with advice on layup, hull performance and how best to return vessels to service as quickly and safely as possible. Our solutions include our Intertrac big data suite alongside our extensive in-house biofouling expertise. Intertrac uses billions of AIS data points from vessels in service, mapping their location against global fouling challenge zones to provide a unique customer report to help improve future coating choices for the customer, at the same time as recommending optimal locations for layup. Depending on the fouling conditions, our biocide-free Intersleek scheme offers a range of 45-60 static days. And while conventional biocidal anti-fouling coatings will generally require cleaning prior to returning to service, the low surface energy of Intersleek means that any fouling which might have adhered while static will then self-clean once the vessel re-enters service.”
“The COVID-19 pandemic has created a number of challenges for marine coatings suppliers, most notably as it pertains to logistics as countries have temporarily shut down and slowly re-opened for business,” said Psomas. “At PPG, we are proud of how our supply team experts around the world managed the challenges and were able to maintain the company’s service excellence targets.”
The pandemic impacted both pleasure/private vessels and commercial ships. “Due to the COVID-19 pandemic in the past two years,there was a decline in private demand,” said Shirahat. “On the other hand, the volume of container transportation is growing due to the increased demand for stay-at-home consumers. Because long-term suspension (layup) and docking delay are expected due to fluctuations in physical distribution, reliable antifouling paints that exhibit antifouling properties at the time of berthing are expected to increase. Other than that, business negotiations for newbuilding have stopped, the amount of construction work on hand at newbuilding has decreased, and the existing on-hand works decreased due to schedule adjustments caused overall decrease in annual demand. Regarding the M&R market, there are cases that the crew members are forced to wait before docking due to COVID-19, and depending on the type of ships, rising of sea freight charges delays the timing of docking. As a result, the demand for paints has been pushed back.”
Regions
Asia has dominated demand for new construction and repair for quite some time. “In the newbuilding segment, China leads with a strong orderbook in the bulker and tanker segments and with increasing orders for more advanced ships,” said Psomas. “South Korea continues to construct the majority of technically advanced vessels with a strong presence in offshore and other specialized tonnage. China is also the number one location for the dry dock repair demand.”
“We work with customers all across the world in the different areas of the marine coatings market,” said Birkert. “Some regions have a larger new build demand so it would be no surprise to share that the Asia Pacific region continues to be a large consumer of coatings for that application, supported of course by our highly experienced technical support teams who work with customers to capture efficiency gains. We have continued to secure contracts for a number of new megabox ships with our Intercept 8500 coating, which provides linear polishing. Many of our fouling control systems and services used by customers in dry docking are in high demand across the world. In Europe for example, Greek ferry operator Attica has recently opted to have biocide-free Intersleek 1100SR fouling control system on their passenger vessels.”
“Area of demand differs greatly between newbuilding and maintenance and repair (M&R),” said Shirahata. “In the former case, shipyards are concentrated in East Asia such as China, South Korea and Japan, and approximately 80% of paint demand is concentrated in these countries and regions. On the other hand, in the case of M&R, the docking sites are mainly in China and Asian countries such as Singapore, but the shipping companies that purchase paint materials are concentrated in Europe, Japan and Singapore.”
New Products
There are a number of new products being brought to market this year. “At AkzoNobel - as we celebrate our International brand’s 140th anniversary this year - we remain committed to innovation in order to develop the coatings and solutions that answer the challenges marine operators face today,” said Birkert. “A good example of this is in the development of our SPC systems, including Intercept 8500. It offers up to 35 static days fouling free which is better than conventional silyl technologies. At the same time, ultra-performing Intersmooth 7476Si SPC is a next generation self-polishing Silyl Methacrylate anti-fouling. The product, which is based upon proven resin technology and an optimized biocide package, is formulated to deliver consistent, reliable and industry leading antifouling performance over the dry-docking cycle. The product comes with a guaranteed speed loss threshold of 1.4%. Intersmooth 7200Si SPC meanwhile benefits from higher solids when compared to the current industry benchmark - reducing waste and VOC emissions while improving application efficiency - providing a guaranteed speed loss threshold of 2.5%.”
Nippon Marine Paint launched its FASTAR series, an antifouling paint for ship bottoms in January 2021. It is a product based on the industry’s first coating film surface control technology using hydrophilic hydrophobic nanodomain structure that reduces the amount of elution of the coating film and reduces the amount of biocide elution by up to 50% while also having high antifouling performance. In addition, the patented water trapping technology that reduces the frictional resistance of the hull is also adopted on the surface of the coating film, which makes it possible to reduce fuel consumption by about 8% compared to conventional hydrolysis antifouling paints.
The latest generation PPG SIGMAGLIDE 1290 fouling release hull coating is based on a 100% pure silicone binder system. The biocide-free product helps to improve the vessels’ power performance and support compliance with the IMO’s short term carbon reduction measures by contributing to a significant reduction of CO2 emissions – by up to 25% as compared to conventional antifouling technologies.
The primary difference of PPG SIGMAGLIDE 1290 compared to other coatings is its much lower frictional resistance compared to conventional antifouling coatings, thanks to its very low surface energy, unique property of the 100% silicone material.
PPG SIGMAGLIDE 1290 is completely biocide-free and as such it is unaffected by legislation such as the Biocidal Products Directive and it is tailored to comply with current and future environmental requirements.
The PPG SIGMA SAILADVANCE range is designed for all vessel types and operating speeds and is particularly effective for static conditions because of the engineered Controlled Surface Active Polymer (CSP) composition. These CSPs act as a lubricant on the coating/water interface supporting laminar flow and thereby reducing hull friction when the ship is sailing. The CSPs also create a slippery surface that resists fouling when the ship is not sailing. This extends possible idle time up to 30 days on average without affecting the hull’s performance.
Source:
“This year has been one of continuing recovery for the marine coatings market following the significant challenges posed by the outbreak of the pandemic in 2020,” said Christopher Birkert, Marine marketing manager at AkzoNobel. “As the global vaccine roll-out brings the virus under more control, global trade is increasing by 4%, resulting in more activity in the marine sector. We have seen a recovery of new build contracts – an increase of 4% overall – as well as a more positive sentiment from marine customers.
“We are proud to have supported our customers as we all navigated through the unprecedented events of 2020 together,” said Birkert. “What was really pleasing to see was that our customers continued to embrace innovation in pursuit of performance and more sustainable solutions in the yard and in operation. Drawing on the 140-year legacy of our International brand we continued to deliver cutting-edge products to meet this need, for example Intersmooth 7200Si, which has up to 40% lower VOC emissions per square meters applied than the nearest competitor, as well as the 90-month Intercept 8500, which delivers a guaranteed speed loss of 1.3% over the docking cycle.”
“Business has continued to move back to a normal state in 2021 and the high level of activity in the main shipping markets and in the newbuilding orders create a positive market recovery sign,” noted Ariana Psomas, PPG Global Segment director newbuild and dry dock. “For the most part we continue to remain optimistic about the industry’s resilience and we expect that it will continue to progress on a positive path.
“Above all, the COVID-19 pandemic has shown how quickly things can change and that, while change is difficult, PPG has proven time and again that we have the strength to manage through such situations,” she added. “With a proven track record of over 135 years, we have weathered many crises, and we consistently emerge stronger and better positioned to serve our customers.”
Some growth is being driven by a focus on sustainability and the need for products that reduce environmental impact and improve efficiencies.
“Recently, the management of shipping companies has become strongly Environmental, Social, and Governance (ESG)-oriented,” said Seiichiro Shirahata, president, representative director of the board at Nippon Paint Marine Coatings Co., Ltd. “Expectations for products and services that bring about environmental measures such as improved operational efficiency and fuel saving as well as economic effects are increasing. Adding to it, the International Maritime Organization (IMO) has set a medium-term target of reducing greenhouse gas emissions to half of the 2008 level by 2050. Furthermore, the organization has set a short-term goal of 40% fuel economy improvement by 2030 under the EEXI regulations from 2023. We will keep up with these trends.
“We have always faced environmental regulations to comply as we develop our marine paints,” added Shirahata. “Particularly the regulation in the 1990s on organotin compounds for antifouling paints on the bottom of ship and the EEXI regulation starting from 2023 are environmental regulations based on international treaties, and then we give first priority to comply with these regulations. In addition, there is environmental legislation enacted independently by the government as well, and we must comply with these regulations one by one.”
At AkzoNobel, sustainability is one of its core values and is integrated in everything they do. “Our approach to sustainable business will help us deliver tangible benefits for our customers, society, the environment and our business,” said Birkert. “As the paints and coatings industry’s leader when it comes to sustainability, we’re proud of our rankings across several indices as well as being recognized by EcoVadis with a platinum rating.
“Ocean preservation and supporting our customers and the industry in the carbon neutral journey are at the heart of the International brand and the ethos of AkzoNobel,” said Birkert. “We’re committed to providing our customers with the coatings and solutions to help address their environmental footprint reduction challenge beyond compliance and towards the shipping industry achieving its 2030 carbon neutral ambition.”
He cited Intersleek 1100SR as an example of the company’s commitment to developing products that not only meet the highest of environmental standards but also move the dial in terms of savings for fleet operators.
According to Birkert, it is one of the highest performance fouling control schemes on the market, It offers more than 10 years of performance without the requirement of a recoat and is proven to reduce paint consumption by 77%, VOC by 86% and decrease CO2 emissions by up to 110,000 tons over multiple operation cycles compared to biocidal Self Polishing Copolymer (SPC) technology.
“It is not always easy to predict exactly how regulation will change globally and we always try to match the highest possible standards,” said Birket. “Many countries around the world are looking harder at ways to improve sustainability through legislation. For example, China is looking very strongly at controlling emissions from industry while Korea has insisted that by 2020, 60% of all coatings to ballast tanks are solvent-free.”
“The shipping industry faces a formidable challenge in achieving compliance with the new environmental regulations set by the IMO and adopted in June 2021, which require drastic reductions in both carbon emissions and carbon intensity,” noted Psomas. “The ability to achieve reductions of this magnitude will require new fuels, new vessel designs and installation of energy efficient technologies to achieve radical improvements in operating efficiency.”
According to Psomas, the use of innovative energy efficient technologies is critical for improving operational performance. “The IMO has published a list of approved Energy Efficiency Technologies among which, low friction coatings have been recognized as a technology that can directly shift the power curve.”
In the area of low friction coatings, she noted that studies have concluded that silicone technology stands out compared to antifouling technologies with the ability to significantly decrease hull friction resistance. PPG’s proprietary biocide free silicone technology, PPG SIGMAGLIDE, has been shown to contribute in achieving these targets by reducing the vessel’s power consumption up to 10% and overall emissions during operation by up to 25% compared to a conventional antifouling technology.
Impact of COVID-19
Travel restrictions related to COVID-19 continue to present challenges to the marine and coatings market.
“A significant hurdle has been global travel restrictions that prevented crews and owner representatives from moving around freely to inspect vessels and plan work,” said Birkert. “As during the shipping crisis of 2010, we helped to support our customers with advice on layup, hull performance and how best to return vessels to service as quickly and safely as possible. Our solutions include our Intertrac big data suite alongside our extensive in-house biofouling expertise. Intertrac uses billions of AIS data points from vessels in service, mapping their location against global fouling challenge zones to provide a unique customer report to help improve future coating choices for the customer, at the same time as recommending optimal locations for layup. Depending on the fouling conditions, our biocide-free Intersleek scheme offers a range of 45-60 static days. And while conventional biocidal anti-fouling coatings will generally require cleaning prior to returning to service, the low surface energy of Intersleek means that any fouling which might have adhered while static will then self-clean once the vessel re-enters service.”
“The COVID-19 pandemic has created a number of challenges for marine coatings suppliers, most notably as it pertains to logistics as countries have temporarily shut down and slowly re-opened for business,” said Psomas. “At PPG, we are proud of how our supply team experts around the world managed the challenges and were able to maintain the company’s service excellence targets.”
The pandemic impacted both pleasure/private vessels and commercial ships. “Due to the COVID-19 pandemic in the past two years,there was a decline in private demand,” said Shirahat. “On the other hand, the volume of container transportation is growing due to the increased demand for stay-at-home consumers. Because long-term suspension (layup) and docking delay are expected due to fluctuations in physical distribution, reliable antifouling paints that exhibit antifouling properties at the time of berthing are expected to increase. Other than that, business negotiations for newbuilding have stopped, the amount of construction work on hand at newbuilding has decreased, and the existing on-hand works decreased due to schedule adjustments caused overall decrease in annual demand. Regarding the M&R market, there are cases that the crew members are forced to wait before docking due to COVID-19, and depending on the type of ships, rising of sea freight charges delays the timing of docking. As a result, the demand for paints has been pushed back.”
Regions
Asia has dominated demand for new construction and repair for quite some time. “In the newbuilding segment, China leads with a strong orderbook in the bulker and tanker segments and with increasing orders for more advanced ships,” said Psomas. “South Korea continues to construct the majority of technically advanced vessels with a strong presence in offshore and other specialized tonnage. China is also the number one location for the dry dock repair demand.”
“We work with customers all across the world in the different areas of the marine coatings market,” said Birkert. “Some regions have a larger new build demand so it would be no surprise to share that the Asia Pacific region continues to be a large consumer of coatings for that application, supported of course by our highly experienced technical support teams who work with customers to capture efficiency gains. We have continued to secure contracts for a number of new megabox ships with our Intercept 8500 coating, which provides linear polishing. Many of our fouling control systems and services used by customers in dry docking are in high demand across the world. In Europe for example, Greek ferry operator Attica has recently opted to have biocide-free Intersleek 1100SR fouling control system on their passenger vessels.”
“Area of demand differs greatly between newbuilding and maintenance and repair (M&R),” said Shirahata. “In the former case, shipyards are concentrated in East Asia such as China, South Korea and Japan, and approximately 80% of paint demand is concentrated in these countries and regions. On the other hand, in the case of M&R, the docking sites are mainly in China and Asian countries such as Singapore, but the shipping companies that purchase paint materials are concentrated in Europe, Japan and Singapore.”
New Products
There are a number of new products being brought to market this year. “At AkzoNobel - as we celebrate our International brand’s 140th anniversary this year - we remain committed to innovation in order to develop the coatings and solutions that answer the challenges marine operators face today,” said Birkert. “A good example of this is in the development of our SPC systems, including Intercept 8500. It offers up to 35 static days fouling free which is better than conventional silyl technologies. At the same time, ultra-performing Intersmooth 7476Si SPC is a next generation self-polishing Silyl Methacrylate anti-fouling. The product, which is based upon proven resin technology and an optimized biocide package, is formulated to deliver consistent, reliable and industry leading antifouling performance over the dry-docking cycle. The product comes with a guaranteed speed loss threshold of 1.4%. Intersmooth 7200Si SPC meanwhile benefits from higher solids when compared to the current industry benchmark - reducing waste and VOC emissions while improving application efficiency - providing a guaranteed speed loss threshold of 2.5%.”
Nippon Marine Paint launched its FASTAR series, an antifouling paint for ship bottoms in January 2021. It is a product based on the industry’s first coating film surface control technology using hydrophilic hydrophobic nanodomain structure that reduces the amount of elution of the coating film and reduces the amount of biocide elution by up to 50% while also having high antifouling performance. In addition, the patented water trapping technology that reduces the frictional resistance of the hull is also adopted on the surface of the coating film, which makes it possible to reduce fuel consumption by about 8% compared to conventional hydrolysis antifouling paints.
The latest generation PPG SIGMAGLIDE 1290 fouling release hull coating is based on a 100% pure silicone binder system. The biocide-free product helps to improve the vessels’ power performance and support compliance with the IMO’s short term carbon reduction measures by contributing to a significant reduction of CO2 emissions – by up to 25% as compared to conventional antifouling technologies.
The primary difference of PPG SIGMAGLIDE 1290 compared to other coatings is its much lower frictional resistance compared to conventional antifouling coatings, thanks to its very low surface energy, unique property of the 100% silicone material.
PPG SIGMAGLIDE 1290 is completely biocide-free and as such it is unaffected by legislation such as the Biocidal Products Directive and it is tailored to comply with current and future environmental requirements.
The PPG SIGMA SAILADVANCE range is designed for all vessel types and operating speeds and is particularly effective for static conditions because of the engineered Controlled Surface Active Polymer (CSP) composition. These CSPs act as a lubricant on the coating/water interface supporting laminar flow and thereby reducing hull friction when the ship is sailing. The CSPs also create a slippery surface that resists fouling when the ship is not sailing. This extends possible idle time up to 30 days on average without affecting the hull’s performance.